When it comes to PCB surface finishes, choosing the right process is critical to ensure performance, reliability, and cost-effectiveness. Among the most widely used surface treatments in PCB manufacturing are Immersion Gold (ENIG) and Hot Air Solder Leveling (HASL), often referred to as tin spraying. While both serve to protect the exposed copper and enhance solderability, they differ significantly in terms of process, performance, cost, and application.
This article provides a comprehensive comparison of immersion gold and HASL to help you make an informed decision for your PCB projects.
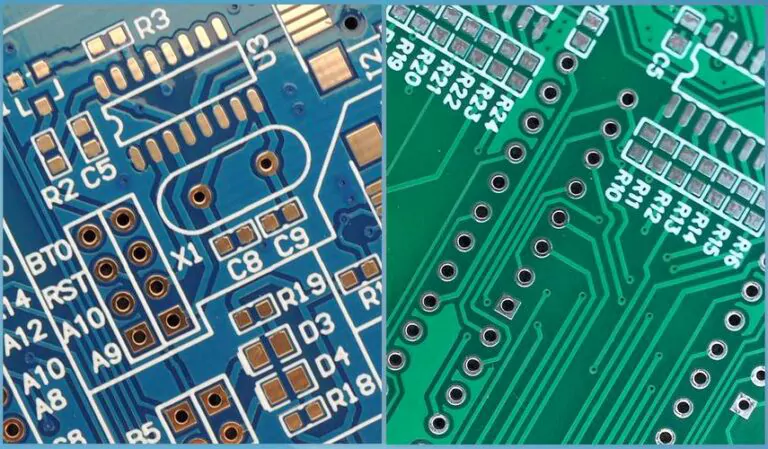
Process Overview
Immersion Gold (ENIG)
This is a chemical deposition method involving two layers: a thin layer of nickel followed by a layer of gold. The process deposits gold onto the surface through an electroless chemical reaction. The result is a flat, uniform, and oxidation-resistant finish ideal for fine-pitch components.
Hot Air Solder Leveling (HASL)
HASL is a physical process where the PCB is dipped into molten tin or tin-lead solder, and excess solder is leveled off using high-pressure hot air. This forms a protective tin coating over the copper pads.
Feature | Immersion Gold (ENIG) | HASL (Tin Spraying) |
Electrical Conductivity | Excellent due to gold’s high conductivity | Good, but slightly lower than gold |
Corrosion Resistance | Superior, gold is highly resistant to oxidation | Moderate, tin is prone to oxidation over time |
Wear Resistance | High; gold surface is hard and durable | Lower; tin is softer and more prone to wear |
Solderability | Excellent, supports multiple soldering cycles | Good, suitable for general soldering tasks |
Surface Flatness | Very flat, ideal for fine-pitch components and BGA packages | Uneven surface may be unsuitable for dense layouts |
Visual Appearance | Shiny gold finish, premium look | Silvery finish, industrial appearance |
Application Areas
Immersion Gold (ENIG) is commonly used in:
High-density interconnect (HDI) PCBs
BGA and fine-pitch components
Gold fingers and edge connectors
High-reliability applications (aerospace, medical, automotive)
HASL (Tin Spraying) is widely used in:
Consumer electronics
Low to medium complexity PCBs
Cost-sensitive projects
Prototyping and mass production
Cost Comparison
ENIG is more expensive due to the use of precious metals and a more complex process.
HASL is significantly more cost-effective, making it ideal for large-volume, budget-focused PCB production.
Environmental Considerations
Immersion Gold involves chemicals like nickel and gold salts, requiring proper waste treatment and environmental controls.
HASL also poses environmental concerns, especially when using leaded solder. Lead-free HASL is a more eco-friendly option but requires precise process control.
Which PCB Surface Finish Should You Choose?
Choose Immersion Gold If: | Choose HASL If: |
Your design includes fine-pitch components or BGA | Your design uses standard pitch components |
You require superior flatness and corrosion resistance | You need a cost-effective solution |
Your product demands high reliability | Your PCB is for general applications or prototypes |
A premium finish is part of your product branding | Budget is a primary concern |
Final Thoughts
Both immersion gold and HASL are well-established PCB surface finish options, each with its own strengths. Choosing between them depends on your specific application requirements, performance expectations, budget, and regulatory compliance needs.
At FAST TURN PCB, we offer both ENIG and HASL surface finishes, allowing you to select the best option for your product. Our expert team is ready to assist with engineering support and fast turnaround times to meet your project goals.
Need help choosing the right surface finish for your PCB?
Contact FAST TURN PCB today for a free consultation or instant quote.